How a Construction Company Achieved 25% Equipment Savings with Dalos
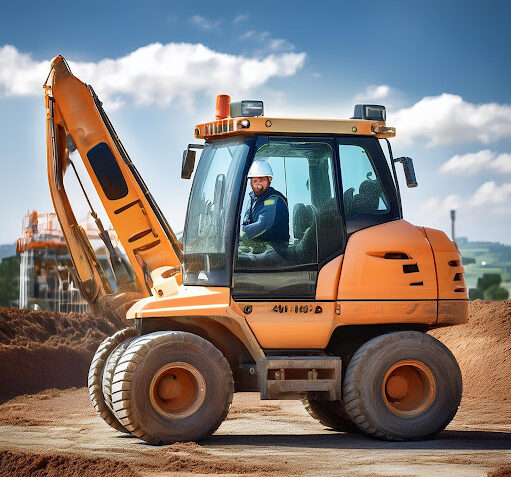
Leveraging Dalos to Achieve Equipment Savings
Managing assets like heavy machinery, tools, and vehicles across multiple job sites is complex. For many construction companies, keeping track of equipment, preventing theft, and ensuring optimal utilization can be a significant challenge—often leading to operational inefficiencies and high equipment costs. In this case study, we’ll explore how one construction firm leveraged Dalos’ Unified Asset Intelligence Platform to achieve equipment savings with Dalos, streamline its asset management processes, prevent equipment losses, and save 25% on equipment costs by optimizing resource allocation and reducing downtime.
Through real-time tracking, predictive maintenance, and better utilization of its assets, this company transformed its operations and achieved significant equipment savings with Dalos.
The Challenge: Managing Assets Across Multiple Job Sites
The construction company in question was a large firm involved in multiple infrastructure and development projects. With projects spread across several locations, it was struggling to manage its assets efficiently. Some of the challenges they faced included:
- Asset Misplacement: With equipment frequently moving between job sites, the company was dealing with misplaced machinery and tools, resulting in project delays as workers searched for missing assets.
- Theft: Valuable equipment left unattended overnight and during off-hours was frequently targeted by thieves, leading to significant financial losses.
- Underutilization: The company was unaware of how its equipment was being used across different job sites. Some assets were underutilized, while others were overworked, leading to uneven wear and tear and higher maintenance costs.
- Unplanned Downtime: Equipment breakdowns were common, causing costly delays and expensive emergency repairs. The firm lacked a predictive maintenance system to detect potential issues before they led to failure.
The Solution: Implementing Dalos for Real-Time Asset Tracking and Monitoring
To address these challenges, the construction firm implemented Dalos’ IoT-powered asset tracking platform across its entire fleet of machinery, tools, and vehicles. The goal was to gain real-time visibility into asset locations, optimize equipment utilization, and reduce operational inefficiencies. Dalos provided the company with a comprehensive solution that included:
Real-Time GPS Tracking
Dalos enabled the company to track the exact location of all assets in real time, ensuring that equipment was always where it needed to be. This reduced the time spent searching for misplaced assets and helped prevent theft.
Geofencing for Theft Prevention
Dalos’ geofencing technology allowed the company to set up virtual boundaries around its job sites. If equipment moved outside of these predefined areas without authorization, Dalos sent instant alerts, allowing the company to take immediate action and prevent theft.
Predictive Maintenance
Dalos’ IoT sensors monitored the performance of the company’s heavy machinery, tracking key metrics such as engine hours, fuel consumption, and temperature. This data allowed the company to perform maintenance proactively, reducing unplanned downtime and extending the lifespan of its equipment.
Usage Reports for Better Resource Allocation
Dalos provided detailed reports on how each piece of equipment was being used across different job sites. This allowed the company to optimize the deployment of its resources, ensuring that underutilized assets were reassigned to areas where they were needed most.
The Results: 25% Equipment Savings With Dalos
After implementing Dalos, the construction company quickly saw significant improvements in its asset management processes. Within the first year, the firm was able to achieve a 25% reduction in equipment costs. Here’s how Dalos helped them achieve this result:
1. Reduced Equipment Rental and Purchase Costs
Before implementing Dalos, the company frequently rented additional equipment to cover gaps caused by misplaced or underutilized assets. Dalos’ real-time tracking allowed the company to locate all equipment instantly, reducing the need for expensive rentals.
Additionally, Dalos’ usage reports enabled the company to identify underutilized assets and redistribute them more effectively across job sites, further reducing the need for new equipment purchases.
Key Savings:
- Lower Rental Costs: With real-time visibility into equipment locations, the company reduced its reliance on rental equipment, cutting rental costs by 15%.
- Optimized Equipment Utilization: By redistributing underutilized assets, the company avoided purchasing unnecessary machinery, saving on capital expenditures.
2. Theft Prevention and Reduced Losses
Equipment theft had been a significant issue for the company, resulting in both financial losses and project delays. With Dalos’ geofencing technology, the company set up virtual boundaries around its job sites and storage areas. Anytime equipment moved outside of these boundaries without authorization, Dalos sent an alert, allowing the company to respond quickly. This system significantly reduced theft incidents.
Key Savings:
- Lower Theft-Related Costs: The implementation of geofencing led to a 35% reduction in theft-related losses, saving the company thousands of dollars in replacement costs.
- Reduced Insurance Premiums: By reducing theft incidents, the company was able to negotiate lower insurance premiums, further contributing to equipment savings with Dalos.
3. Reduced Downtime with Predictive Maintenance
Unplanned equipment breakdowns were a frequent cause of project delays and high repair costs. Dalos’ predictive maintenance feature allowed the company to monitor the health of its equipment in real time. The system detected early signs of wear and tear, such as abnormal temperature fluctuations or increased fuel consumption, enabling the company to schedule maintenance before equipment failed.
Key Savings:
- Lower Repair Costs: By addressing maintenance needs proactively, the company reduced the frequency of emergency repairs, cutting repair costs by 20%.
- Increased Equipment Uptime: Preventive maintenance reduced equipment downtime by 30%, allowing the company to keep projects on schedule and avoid costly delays.
4. Improved Resource Allocation and Efficiency
Dalos’ detailed usage reports gave the construction company insight into how often each piece of equipment was being used. This data allowed managers to make informed decisions about resource allocation, ensuring that all assets were used efficiently across different job sites. By optimizing equipment utilization, the company was able to complete projects more quickly and reduce operational costs.
Key Savings:
- Maximized Equipment Utilization: The company improved equipment utilization by 25%, ensuring that machinery was fully deployed across all projects, reducing idle time and increasing productivity.
- Lower Fuel and Operational Costs: By using Dalos to optimize equipment routes and usage, the company was able to reduce fuel consumption and operational costs, contributing to further savings.
A 25% Reduction in Equipment Costs with Dalos
By implementing Dalos’ Unified Asset Intelligence Platform, the construction company was able to transform its asset management processes, reduce inefficiencies, and achieve a 25% equipment savings within the first year. The real-time visibility provided by Dalos allowed the company to:
- prevent theft
- reduce downtime
- optimize resource allocation
- avoid unnecessary equipment rentals and purchases
With improved operational efficiency and better control over its assets, the company continues to see long-term returns on its investment in Dalos, making it a vital tool for managing complex construction projects in today’s competitive industry.
Key Benefits of Dalos for Construction Companies:
- Real-time GPS tracking for instant equipment location
- Geofencing technology to prevent theft and unauthorized movement
- Predictive maintenance to reduce downtime and extend equipment lifespan
- Detailed usage reports for optimized resource allocation and equipment utilization